Why calibration is important?
Calibration defines the accuracy and quality of measurements recorded using a piece of equipment. Over time there is a tendency for results and accuracy to 'drift' when using particular technologies or measuring particular parameters such as temperature and humidity.
What is Calibration?
Calibration involves comparing an instrument's measurement to a standard measurement and making adjustments using a calibrator to eliminate any discrepancies. This process is essential to maintain the accuracy and reliability of instruments, whether they are used in laboratories, factories, or medical facilities.

The Significance of Calibration
Calibration is a fundamental aspect of ensuring accuracy, reliability, and efficiency across various fields. It is the process of adjusting and verifying the accuracy of a measuring instrument by comparing it with a known standard. Here, we will explore the profound significance of calibration and why it is indispensable in numerous industries.
Accuracy in Measurements
At the heart of calibration lies the quest for accuracy. Precise measurements are critical in scientific research, engineering, manufacturing, healthcare, and many other fields. Calibration ensures that instruments provide accurate readings, which is essential for:
- Scientific Research: Accurate data is crucial for experiments and studies, impacting the validity and reproducibility of scientific findings.
- Engineering and Manufacturing: Precise measurements ensure that parts and products are manufactured to exact specifications, reducing defects and enhancing quality.
- Healthcare: In medical diagnostics and treatment, accurate readings from instruments like thermometers, blood pressure monitors, and imaging devices are vital for patient care.
Ensuring Safety and Compliance
Calibration is a key factor in maintaining safety and regulatory compliance. Many industries are governed by strict standards and regulations that mandate regular calibration of instruments:
- Healthcare: Ensures patient safety by providing accurate diagnostic results and administering correct dosages of medication.
- Aerospace: Guarantees the safety of aircraft operations by ensuring that instruments like altimeters, airspeed indicators, and navigation systems are accurate.
- Environmental Monitoring: Accurate measurements of pollutants and environmental parameters are crucial for compliance with environmental regulations and ensuring public health.
Enhancing Product Quality
Calibration directly impacts product quality and consistency. In manufacturing, for instance, calibrated instruments ensure that production processes yield products that meet predefined quality standards:
- Consistency: Ensures that each product or batch meets the same quality criteria, leading to customer satisfaction and brand loyalty.
- Reduction of Waste: Minimizes material waste and rework by ensuring that processes are within tolerance limits.
- Improved Efficiency: Enhances operational efficiency by reducing downtime and maintaining smooth production flows.

Calibration in Different Industries
Calibration is a critical process in various industries to ensure accuracy and reliability of measurements and instruments.
Calibration in Manufacturing
In manufacturing, the importance of calibration cannot be overstated. It ensures that machinery and equipment produce components and products that meet stringent quality standards. For instance:
- Automotive Industry: Ensures that parts like engines and braking systems are manufactured with precision, contributing to vehicle safety and performance.
- Food and Beverage: Ensures that processes like filling, packaging, and labeling are accurate, maintaining product quality and regulatory compliance.
Calibration in Healthcare
In healthcare, calibration is critical for ensuring accurate diagnostic and therapeutic outcomes. Examples include:
- Diagnostic Instruments: Ensures that equipment like X-ray machines, MRI scanners, and blood analyzers provide accurate results.
- Therapeutic Devices: Ensures that devices like infusion pumps and radiation therapy machines deliver precise treatments.
Calibration in Aerospace
The aerospace industry relies heavily on precise measurements to ensure the safety and performance of aircraft and spacecraft. Calibration in this sector includes:
- Flight Instruments: Ensures that instruments used by pilots, such as altimeters and airspeed indicators, are accurate.
- Navigation Systems: Ensures that GPS and other navigation systems provide precise location and route information.
Calibration in Research and Development
In R&D, accurate measurements are the backbone of innovation and discovery. Calibration in this context ensures:
- Validity of Results: Ensures that experimental data is accurate and reproducible.
- Advancements in Technology: Supports the development of new technologies by providing reliable measurement data.

Benefits of Regular Calibration
Regular calibration of instruments and equipment provides numerous benefits across various industries. Here are some key advantages:
- Improved Efficiency
Regular calibration ensures that instruments function efficiently, reducing downtime and increasing productivity. It helps in identifying potential issues before they escalate, ensuring smooth operations.
- Cost Savings
While calibration involves an initial cost, it ultimately saves money by preventing costly errors, reducing waste, and extending the lifespan of equipment.
- Enhanced Reputation and Trust
Consistently calibrated instruments build trust with clients and stakeholders by ensuring reliable and high-quality outputs. This enhances the reputation of businesses and organizations.
Conclusion
In conclusion, calibration is a fundamental process that ensures the accuracy, safety, and efficiency of instruments across various industries. From manufacturing to healthcare, the significance of calibration cannot be overstated. Regular calibration not only improves product quality and operational efficiency but also builds trust and compliance with industry standards. As technology continues to evolve, the future of calibration holds exciting possibilities for even greater precision and reliability.
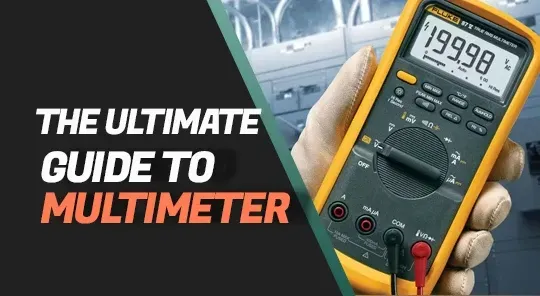
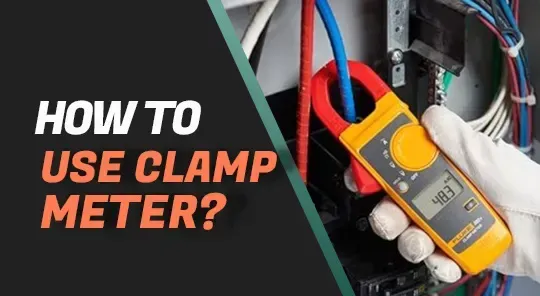
