Best Guide on Compressed air meters
A complete guide to the compressed air meter
Compressed air is a versatile and common source of energy in numerous industrial applications. It plays a pivotal role in various production processes, from driving machines to managing systems. Given its widespread use and significance, accurate monitoring and measurement of compressed air consumption are crucial for enhancing efficiency, detecting potential leaks, and reducing operating costs. This is where compressed air meters, also known as flow meters, come into play.
This comprehensive guide will cover everything you need to know about compressed air meters. We'll delve into what they are, how they work, their benefits, considerations for choosing the right meter, and best practices for installation and maintenance.
What Are Compressed Air Meters?
Compressed air meters, also referred to as flow meters, are devices designed to measure the flow rate and volume of compressed air. They provide valuable insights into the efficiency of compressed air systems, consumption trends, and usage patterns. By monitoring and analyzing this data, industries can make informed decisions regarding system upgrades, maintenance schedules, and energy-saving initiatives.
How Do Compressed Air Meters Operate?
Compressed air meters employ various technologies to measure the flow rate of compressed air accurately. Here are some of the commonly used types of meters:
1. Differential Pressure (DP) Meters:
DP meters measure the difference in air pressure across a restricted space, such as a venturi or orifice plate. These meters correlate the pressure drop with the flow rate, making them highly accurate for measuring compressed air usage, especially in applications where precision is crucial and the flow range is moderate.
2. Thermal Mass Flow Meters:
Thermal mass flow meters gauge the cooling effect of compressed air on a heated sensing element to estimate the flow rate. As the flow rate increases, more heat is removed, allowing the meter to accurately determine mass flow. These meters offer excellent accuracy and stability and can measure both low and high flow rates effectively.
3. Vortex Shedding Meters:
Vortex shedding meters operate based on the principle of vortex shedding. When compressed air flows past a bluff body inserted into the flow, alternating vortices are generated. The bluff body oscillates due to these vortices, and the frequency of oscillation is inversely proportional to the flow rate. By monitoring the frequency of vortices, the meter can determine the flow rate. Vortex shedding meters are known for their reliability and wide dynamic range.
4. Ultrasonic Flow Meters:
Ultrasonic flow meters measure the velocity of compressed air moving through a pipe using ultrasonic signals. These meters calculate the flow rate by comparing the transit times of ultrasonic signals upstream and downstream. Ultrasonic flow meters are suitable for measuring large pipe diameters and high flow rates without invasive procedures.
Considerations for Choosing a Compressed Air Meter
Selecting the right compressed air meter for your application requires careful consideration of several factors:
1. Accuracy Requirements:
Determine the level of precision needed for your measurements based on your specific application. Some applications may tolerate a degree of flexibility in accuracy, while others demand high precision. Consider factors such as overall meter accuracy, repeatability, and calibration cycles.
2. Minimum and Maximum Flow Rates:
Identify the minimum and maximum flow rates that your meter must monitor accurately. Ensure that the selected meter can handle the anticipated flow range of your compressed air system. If your system encompasses a wide range of flow rates, choose a meter that can provide precise measurements across the entire range.
3. Temperature and Pressure:
Take into account the operational pressure and temperature parameters of your compressed air system. Ensure that the chosen meter is compatible with these conditions to ensure accurate measurements and reliable performance. Some meters may have limitations regarding pressure and temperature ranges, so choose accordingly.
4. Installation Requirements:
Consider installation requirements such as pipe diameter, orientation, and available space. Some meters may necessitate specific pipe arrangements or straight pipe runs for accurate readings. Choose a meter that can be installed correctly within the physical constraints of your installation location.
5. Communication and Integration:
Determine whether you require a meter with communication capabilities to integrate with your control systems or data monitoring platforms. Communication-enabled meters facilitate data collection, analysis, and seamless integration into your existing infrastructure. Look for meters that support communication protocols relevant to your application.
Benefits of Compressed Air Meters
Utilizing compressed air meters offers several advantages to industrial processes:
1. Energy Efficiency:
Compressed air meters enable precise monitoring of compressed air usage, helping identify areas of high consumption and potential leaks. Operators can implement energy-saving measures, improve system performance, and reduce energy costs. By monitoring flow rates and compressed air volume, businesses can detect inefficient equipment, locate leaks, and take corrective actions to minimize energy losses.
2. Maintenance Optimization:
Continuous monitoring of compressed air flow and pressure enables proactive maintenance. Meters help identify unusual patterns, pressure drops, or excessive fluctuations, alerting operators to the need for maintenance or repairs before critical failures occur. Regular maintenance and timely repairs can prevent costly downtime and ensure the reliability of the compressed air system.
3. Cost Reduction:
Compressed air meters assist in reducing waste and operating expenses by detecting inefficiencies and leaks. They provide data for informed decisions regarding system upgrades, leak detection campaigns, and equipment updates. Businesses can identify energy-intensive equipment or processes and take steps to enhance their performance, resulting in cost savings, thanks to reliable measurements of compressed air consumption.
4. Reporting and Compliance:
Meters offer precise and dependable data on compressed air consumption, which is essential for complying with regulations, disclosing environmental impact, and demonstrating sustainability efforts. Many industries face environmental regulations that require them to report energy usage and carbon footprint. Compressed air meters provide the necessary data to comply with these regulations and showcase environmental responsibility.
Installation and Maintenance Best Practices
To ensure that compressed air meters provide accurate readings and consistent performance, they must be installed and maintained correctly. Here are some best practices to follow:
1. Proper Installation:
Install the meter following the manufacturer's instructions and recommendations. Consider factors such as upstream and downstream plumbing, pipe size, straight pipe runs, and flow conditioning requirements. Before using the meter, ensure it has been accurately calibrated and zeroed.
2. Regular Calibration:
Calibrate the meter periodically to maintain accuracy. Calibration ensures that the meter's readings align with established standards, instilling confidence in the reliability of the generated data. Consider using accredited calibration services for traceable results and adhere to the manufacturer's guidelines for calibration frequency.
3. Annual Preventative Maintenance:
Implement an annual preventative maintenance schedule for your compressed air meter. Regularly inspect the meter for signs of wear, contamination, or damage. Clean the meter and its components as per the manufacturer's instructions. Ensure that all connections are tightly sealed to prevent air leaks that can affect the meter's performance.
4. Leak Detection:
Compressed air leaks can waste energy and significantly impact the accuracy of meter readings. Establish a leak detection program to swiftly identify and rectify leaks. Conduct routine inspections and utilize appropriate equipment, such as ultrasonic leak detectors often integrated with compressed air meters, to locate and address system leaks.
5. Analyze Usage Trends:
Utilize the data collected from the compressed air meter to analyze usage trends, identify inefficiencies, and generate accurate reports. Employ software or data visualization tools to monitor trends, track energy consumption, and identify potential opportunities for improvement. Regularly produce reports on compressed air usage, energy savings, and maintenance activities to track progress and inform stakeholders.
TESTO 6443 Compressed Air Meter: Key Features
Now, let's explore one of the popular brands in compressed air meters and review the key features of the TESTO 6443 Compressed Air Meter:
1. High Precision Measurements:
The TESTO 6443 Compressed Air Meter provides precise and reliable measurements thanks to its high-precision sensors and advanced measuring algorithms. This level of accuracy enables organizations to gain a clear understanding of their compressed air usage, allowing them to identify inefficiencies, optimize energy use, and reduce operational costs.
2. Broad Flow Range:
The TESTO 6443 is capable of measuring a wide range of flow rates, making it suitable for various industrial applications. Whether you need to measure low flow rates for precise processes or high flow rates for demanding applications, this meter can accommodate a range of needs. Its versatility ensures comprehensive data collection and analysis across diverse processes.
3. Data Display and User-Friendly Interface:
Featuring an intuitive user interface, the TESTO 6443 Compressed Air Meter offers easy setup and operation. The meter is equipped with a clear LCD screen that displays real-time data, allowing users to monitor compressed air flow and consumption effortlessly. The user-friendly interface streamlines installation, enabling businesses to start monitoring their compressed air systems promptly.
4. Data Logging and Reporting:
One of the standout features of the TESTO 6443 is its data logging capability. The meter can continuously record and retain data related to flow rates, pressure differentials, and energy usage. This empowers organizations to review historical data, identify trends or patterns in their compressed air usage, and generate comprehensive reports. These reports are valuable for in-depth analysis, compliance with industry standards, and fulfilling legal obligations. They prove particularly useful in audits, energy management plans, and decision-making processes for optimizing compressed air systems.
5. Connectivity and Integration:
The TESTO 6443 Compressed Air Meter offers connectivity and integration options to enhance its performance in industrial settings. The meter seamlessly interfaces with existing control systems and energy management software, enabling automated data integration. This integration provides organizations with a consolidated view of their energy usage, including compressed air, facilitating informed decisions related to energy-efficient maintenance and optimization.
6. Robust Design:
Built to withstand challenging industrial conditions, the TESTO 6443 is constructed using durable materials. It can operate in extremely cold environments, endure moisture and dust, and withstand vibrations, ensuring reliable operation even in harsh conditions. The meter's durability minimizes the risk of environmental disturbances or measurement errors, ensuring accurate readings consistently.
In Conclusion
In summary, compressed air meters play a vital role in industries reliant on compressed air systems. These meters empower businesses to optimize energy usage, reduce costs, and enhance overall efficiency by accurately measuring and monitoring compressed air flow. When selecting a compressed air meter, consider factors such as accuracy, flow range, compatibility with pressure and temperature conditions, installation requirements, and integration possibilities. Accurate readings and dependable performance depend on proper installation, regular calibration, and preventative maintenance.
The TESTO 6443 Compressed Air Meter stands out as a robust and reliable tool for tracking compressed air usage. With its high precision, broad flow range, user-friendly interface, data logging capabilities, integration options, and robust construction, it provides businesses with the insights needed to improve their compressed air systems and enhance operational efficiency.
Incorporating the right compressed air meter into your industrial processes allows you to discover inefficiencies, detect leaks, implement preventative maintenance plans, and make informed decisions that benefit your operations, productivity, and sustainability efforts. Compressed air meters are indispensable instruments for industries seeking to optimize their energy usage and reduce costs effectively.
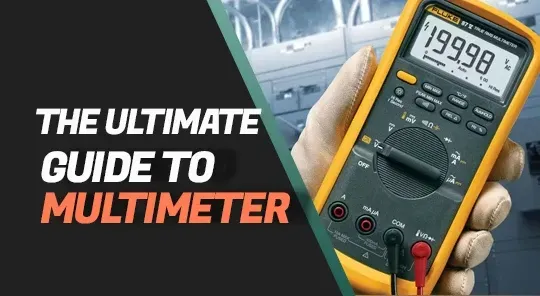
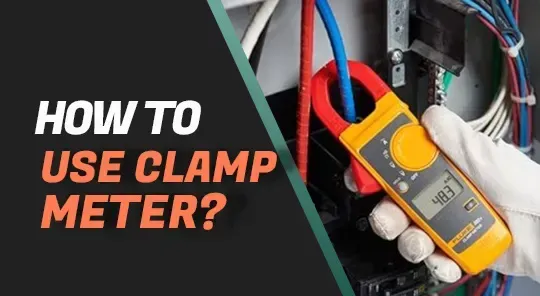
